Users can explore printing rigid 316L stainless steel parts for industrial applications alongside advanced engineering polymers and composites on METHOD with the MakerBot LABS Experimental Extruder
BROOKLYN, N.Y. — (BUSINESS WIRE) — February 16, 2021 — MakerBot, a Stratasys company (Nasdaq: SSYS), today announced that the BASF Ultrafuse® 316L Stainless Steel material by Forward AM has been qualified for the MakerBot LABS™ Experimental Extruder1 for the MakerBot METHOD® 3D printers. With an open materials platform and a growing portfolio of advanced engineering-grade materials, METHOD is now the only industrial desktop 3D printer in its price-class with a heated chamber that can print polymer, composite, and metal materials.
This press release features multimedia. View the full release here: https://www.businesswire.com/news/home/20210216005468/en/
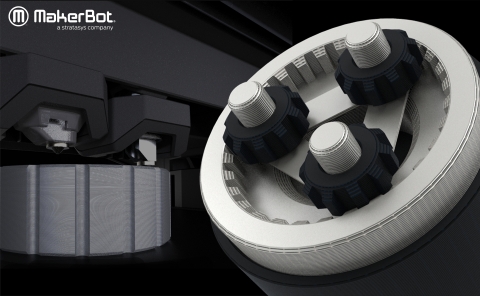
MakerBot METHOD now prints BASF Ultrafuse 316L Stainless Steel material by Forward AM (Photo: Business Wire)
Ultrafuse® 316L Stainless Steel material combines high strength, rigidity and durability needed for a range of applications including functional prototypes and manufacturing tools. Available using the MakerBot LABS GEN 2 Experimental Extruder, this metal-polymer composite material provides METHOD users with an accessible and cost-effective option to experiment with metal 3D printing applications without making the significant investment typically needed for a dedicated metal 3D printing solution. 3D printing stainless steel parts can also shorten the time it takes to produce parts, further reducing operational costs compared to traditional methods. METHOD’s heated chamber and ability to control the speed at which a part cools down during the printing process can also help reduce the risk of delamination.
Once the part is printed with BASF Forward AM Ultrafuse® 316L, it can then be sent out to post-processing or specialized manufacturing facilities for debinding and sintering, which turns the part printed with the composite material into solid stainless steel. This process allows users to create stainless steel parts without investing in expensive debinding and sintering equipment. Final parts can achieve up to 96%2 of the density of pure 316L metal material. Users can produce lightweight, hollow metal parts with high tensile strength compared to polymers that would be difficult to produce in other ways.
“Ultrafuse Metal Filaments removed the barriers between metal 3D printing and users to make the technology more accessible to a larger audience. We are very excited to have our Ultrafuse 316L part of the MakerBot LABS program. We aim to add our recently launched Ultrafuse 17-4 PH filament, with the Ultrafuse 316L to make our entire portfolio accessible to MakerBot users,” said Firat Hizal, Head of Metal Systems Group, BASF 3D Printing Solutions.
"We are excited to have MakerBot METHOD 3D printers join the metal 3D printing ecosystem that we've built alongside BASF Forward AM. Making 3D printing more accessible has always been a major goal at MatterHackers, and having reliable desktop printers like the METHOD and METHOD X that are capable of printing real metal parts affordably is a huge step forward," said Dave Gaylord, vice president of Product and Technology at MatterHackers.
“Our customers have expressed interest in exploring metal 3D printing but have been deterred by the high costs and extensive processes of traditional metal 3D printing solutions. By supporting a metal filament as part of the MakerBot LABS program, customers now have an easier and more affordable way to experiment with 3D printing metal before investing in a full printing, debinding, and sintering solution,” said Johan-Till Broer, vice president of Product Development, MakerBot.
Ultrafuse® 316L material properties make it ideal for a variety of manufacturing tools, jigs and fixtures, and end-use parts, such as workholdings that need to withstand high temperatures; brackets that require high strength and custom designs for specialty machinery; or robotic grippers that need to be strong, lightweight, and wear resistant.
Processing tickets for debinding and sintering are available through MatterHackers, a leading material and 3D printer reseller in the U.S. MatterHackers is an Ultrafuse® 316L authorized reseller, and also offers build plate adhesives needed to print the material and design consultation, which is highly recommended due to the special design requirements for this material.
Ultrafuse® 316L and additional debinding and sintering options are available through authorized resellers.
The MakerBot LABS GEN 2 Experimental Extruder enables users to print with a diverse list of third-party materials on METHOD, opening the possibilities of new and different applications. With the METHOD platform, users can print engineering-grade plastics and carbon fiber materials, while also exploring applications with experimental metal 3D printing solutions. METHOD’s modular platform lets users easily switch between six different extruders that allow them to print different base and model materials. MakerBot is continuing to identify additional industrial 3D printing materials for the METHOD platform.
For more information, visit http://www.makerbot.com/metal.
About MakerBot
MakerBot, a Stratasys company, is a global leader in the 3D printing industry. The company helps create the innovators of today and the businesses and learning institutions of the future. Founded in 2009 in Brooklyn, NY, MakerBot strives to redefine the standards for 3D printing for reliability, accessibility, precision, and ease-of-use. Through this dedication, MakerBot has one of the largest install bases in the industry and also runs Thingiverse, the largest 3D printing community in the world.
To learn more about MakerBot, visit makerbot.com, the MakerBot blog, Twitter, LinkedIn, or Facebook. Stratasys (parent company of MakerBot) reserves the right to utilize any of the foregoing social media platforms, including the company's websites, to share material, non-public information pursuant to the SEC's Regulation FD. To the extent necessary and mandated by applicable law, Stratasys will also include such information in its public disclosure filings.
MakerBot, MakerBot LABS, MakerBot METHOD, METHOD, MakerBot METHOD X and METHOD X are trademarks or registered marks of MakerBot Industries, LLC. All other trademarks are the property of their respective owners.
1 The MakerBot LABS Experimental Extruder for METHOD is an experimental product and is not covered under limited warranty or MakerCare.
2 Result is based on testing conducted by Forward AM on the METHOD 3D printer with Ultrafuse® 316L material and specified print parameters
View source version on businesswire.com: https://www.businesswire.com/news/home/20210216005468/en/
Contact:
Bennie Sham
MakerBot
bennie.sham@makerbot.com