With 316L, Businesses Can Produce Cost-Effective, End-Use Metal Parts for Extreme Temperature, Highly Corrosive Applications on the World’s Fastest Metal 3D Printing Platform
BOSTON — (BUSINESS WIRE) — April 21, 2021 — Desktop Metal (NYSE: DM), a leader in mass production and turnkey additive manufacturing solutions, today announced it has qualified the use of 316L stainless steel for the Production System™ platform, which leverages patent pending Single Pass Jetting™ (SPJ) technology designed to achieve the fastest build speeds in the metal additive manufacturing market.
This press release features multimedia. View the full release here: https://www.businesswire.com/news/home/20210421005612/en/
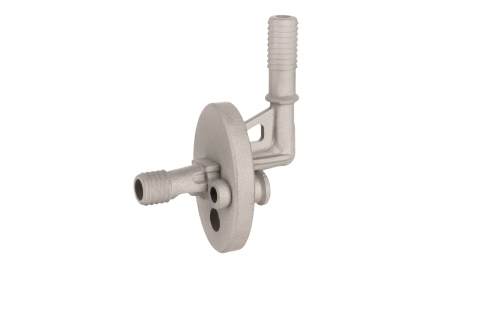
The Production System platform enables printing this heavy industry fluid connector in 316L stainless steel as a single, consolidated component and can support a throughput of nearly 5,500 parts per week. (Photo: Business Wire)
Known for its corrosion resistance and excellent mechanical properties at extreme temperatures, 316L stainless steel is well suited for applications in the most demanding conditions, such as parts exposed to marine or pharmaceutical processing environments, food preparation equipment, medical devices and surgical tooling. It also exhibits excellent weldability by standard fusion and resistance methods.
“The qualification of 316L stainless steel with leading mechanical properties on the Production System platform is part of our aggressive roadmap to support an array of materials for binder jetting and a testament to the advantages of SPJ technology, which enables mass production throughput without sacrificing part performance and repeatability,” said Jonah Myerberg, co-founder and CTO of Desktop Metal. “With 316L on the Production System P-50, businesses will now be able to leverage additive manufacturing to produce complex, end-use parts suitable for use in harsh environments at volumes and costs competitive with conventional manufacturing.”
316L Stainless Steel - Key Applications
Through extensive testing, the Desktop Metal materials science team has validated that 316L stainless steel printed on Production System technology and sintered by Desktop Metal meets MPIF 35 standards for structural powder metallurgy parts set by the Metal Powder Industries Federation. Parts printed with 316L have demonstrated excellent mechanical properties and corrosion resistance, while significantly decreasing production time and part cost.
-
Rocker Arm for Salt Water Marine Environments
Rocker arms are used to open and close intake and exhaust valves on an outboard marine engine. The use of 316L extends the part’s life and provides corrosion resistance against harsh salt water environments. Manufacturing on the Production System P-50 enables the production of more than a thousand parts per day with ribbing features and cutouts to deliver adequate strength and stiffness while maintaining low weight and a small footprint versus the standard cast alternatives, which require up to 8 to 14 weeks lead time.
-
Fluid Connector for Chemical Processing Plants
Heavy industry fluid connectors used in many chemical processing plants need to be manufactured in 316L for corrosion resistance against the chemicals moving through the part. The connector’s complex internal channels make it impossible to manufacture as a single component via conventional manufacturing methods. The Production System P-50 enables printing the fluid connector in 316L as a single, consolidated component and can support a throughput of nearly 5,500 parts per week, at a fully burdened cost of approximately $6.85 per part.
-
Customized Surgical Tool for Medical Applications
Because 316L is a surgical-grade steel, it is an ideal material for medical applications like surgical nozzles. By eliminating tooling, additive manufacturing enables mass production runs of different sized nozzles with no lead time, featuring internal channels that are optimized for individual patient needs. Printing on the Production System P-50 eliminates multiple fixturing steps otherwise required for machining, and results in a throughput of more than 24,000 parts per week at approximately $2.50 per part. By comparison, machining the same part would cost $20.00 -$40.00 per part, and require up to two months to create the same number of parts the P-50 can produce in just one week.
-
Gear Shift Knob for the Automotive Industry
High touch parts like this gear knob require materials that are easy to sanitize. 316L is an optimal material choice because it offers excellent corrosion resistance and cleans easily. This textured gear shift is an example of mass customization made possible by binder jetting on the Production System, which supports up to 200 parts per build and up to 6,700 parts per week. By comparison, casting would require 8 to 14 weeks lead time for tooling, just to begin volume production.
“As innovators in the automotive, medical, consumer products and petrochemical industries continue to embrace the benefits of additive manufacturing, implementing applications made possible with 316L stainless steel, we will begin to see even more widespread adoption of binder jetting technology,” said Myerberg. “Materials that push the boundaries of what AM technology can do will continue to advance the industry and drive unparalleled throughput while significantly reducing cost and waste.”
The Production System - the World’s Fastest Way to 3D Print Metal Parts At-Scale
Created by the inventors of binder jetting and single-pass inkjet technology, the Production System is an industrial manufacturing platform powered by Desktop Metal’s SPJ technology. It is designed to achieve speeds up to 100 times those of legacy powder bed fusion additive manufacturing technologies and enable production quantities of up to millions of parts per year at costs competitive with conventional mass production techniques. The Production System platform consists of two printer models: the P-1, a solution for process development and serial production applications, and the P-50, a large form factor mass production solution for end-use parts, scheduled to begin commercial shipments in 2021. The Production System combines Desktop Metal engineered binders with an open material platform, allowing customers to produce high performance parts using the same low-cost metal powders used in the Metal Injection Molding (MIM) industry. An inert processing environment enables compatibility with a variety of materials, including the now qualified 316L stainless steel as well as high-performance alloys and even reactive metals, such as aluminum and titanium.
For more information on the Production System platform, visit https://www.desktopmetal.com/products/production.
About Desktop Metal
Desktop Metal, Inc., based in Burlington, Massachusetts, is accelerating the transformation of manufacturing with an expansive portfolio of 3D printing solutions, from rapid prototyping to mass production. Founded in 2015 by leaders in advanced manufacturing, metallurgy, and robotics, the company is addressing the unmet challenges of speed, cost, and quality to make additive manufacturing an essential tool for engineers and manufacturers around the world. Desktop Metal was selected as one of the world’s 30 most promising Technology Pioneers by the World Economic Forum and named to MIT Technology Review’s list of 50 Smartest Companies. For more information, visit www.desktopmetal.com.
Forward-looking Statements
This press release contains certain forward-looking statements within the meaning of the federal securities laws. Forward-looking statements generally are identified by the words “believe,” “project,” “expect,” “anticipate,” “estimate,” “intend,” “strategy,” “future,” “opportunity,” “plan,” “may,” “should,” “will,” “would,” “will be,” “will continue,” “will likely result,” and similar expressions. Forward-looking statements are predictions, projections and other statements about future events that are based on current expectations and assumptions and, as a result, are subject to risks, uncertainties. Many factors could cause actual future events to differ materially from the forward-looking statements in this document, including but not limited to, the risks and uncertainties set forth in Desktop Metal, Inc.'s filings with the U.S. Securities and Exchange Commission. These filings identify and address other important risks and uncertainties that could cause actual events and results to differ materially from those contained in the forward-looking statements. Forward-looking statements speak only as of the date they are made. Readers are cautioned not to put undue reliance on forward-looking statements, and Desktop Metal, Inc. assumes no obligation and does not intend to update or revise these forward-looking statements, whether as a result of new information, future events, or otherwise.
View source version on businesswire.com: https://www.businesswire.com/news/home/20210421005612/en/
Contact:
Press
Lynda McKinney
lyndamckinney@desktopmetal.com
978-224-1282