New polyethersulfone material improves cycle times & lowers tooling costs
CLINTON, Tenn. — (BUSINESS WIRE) — July 12, 2021 — When a major aerospace OEM needed a thermally conductive, autoclavable resin to advance the performance of 3D-printed composite molds for compression molding, it turned to its go-to materials design partner –– Techmer PM LLC.
This press release features multimedia. View the full release here: https://www.businesswire.com/news/home/20210712005294/en/
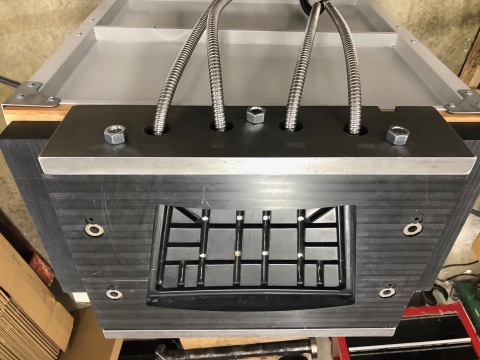
Additive manufactured compression molding tool made using Techmer PM's Electrafil® PESU 1815 3DP resin. (Photo credit: Thermwood Corp.)
Techmer PM took up the challenge in late 2018, and just announced it is commercializing a new polyethersulfone (PESU) resin that is up to the task. Called Electrafil® PESU 1815 3DP, the product offers enhanced thermal conductivity to improve processing and cycle times at temperatures up to 350º F, while maintaining properties critical to the additive manufacturing (AM) and composite curing processes.
“The resin,” notes Techmer New Markets Technology Leader Alan Franc, “offers a greater than 250 percent improvement in X-, Y-, and Z- direction thermal conductivities compared to conventional reinforced PESU AM tooling compounds. At the same time, it maintains similar modulus and heat-deflection temperature under load properties.”
Curing a thermoset part via autoclave typically can take anywhere between two and 12 hours, but the greater thermal conductivity of Electrafil® PESU 1815 3DP promises to shorten those cycle times by accelerating the heating and cooling process.
Additionally, Franc said, the material is proving capable of replacing more expensive metal tooling for use in compression molding, which can bring down tooling costs and enable more-frequent, cost-effective design changes.
By creating molds using additive manufacturing, tool designers can drastically reduce the development time from the initial concept to finished product. 3D printing the approximate tool shape and then milling to the final shape generally can be completed in weeks rather than the months needed with traditional methods. Techmer PM’s new technology will further boost the speed to market by accelerating the curing time of the final composite.
Researchers at the Department of Energy’s Manufacturing Demonstration Facility at Oak Ridge National Laboratory (ORNL) collaborated with Techmer PM in the development process by providing vital 3D printing and testing services. “We see strong market potential for this technology in sectors such as aerospace and automotive,” said Vlastimil Kunc, ORNL’s group leader of advanced composites manufacturing.
Franc noted that a major aerospace OEM is currently evaluating the effects of increased thermal conductivity on accelerating autoclave curing cycles. The project is running at pilot scale now, producing validation samples for that customer, with results expected later this year.
Additionally, he said, a university is studying the effect of enhanced thermal conductivity on the compression molding of composites, especially in machines that only use heated platens to heat the mold.
Techmer PM’s collaboration with ORNL continues to produce valuable results.
“A few years ago,” Franc said, “people thought you couldn’t use plastic tooling in an autoclave,” assuming it would melt or deform. But Techmer developed an initial PESU material, called Electrafil® PESU 1810 3DP, that could withstand the heat. This latest grade, however, looks set to further improve performance and lower the cost, while also being commercially viable as a production tooling material for compression molding.
Techmer PM is seeking additional partners to test and validate the material in these different applications.
About Techmer PM
Founded in 1981, Techmer PM LLC is a materials design company that specializes in modifying and fine-tuning the properties of technical polymers. The Clinton, Tenn.-based company thrives on partnering and collaborating with plastics processors, fabricators, designers, specifiers, and brand owners. Drawing on a broad portfolio of resins –– from polyolefins to PEEK –– Techmer PM helps manufacturers enhance product function and appearance in scores of end-use markets. The award-winning firm operates seven North American plants and has extensive expertise in virtually every plastic- and fiber-related process, from additive manufacturing and blown film to nonwovens, injection molding, and sheet extrusion. Techmer PM has been recognized by Plastics News six times since 2014 as one of the “Best Places to Work” in the North American plastics industry. www.techmerpm.com
View source version on businesswire.com: https://www.businesswire.com/news/home/20210712005294/en/
Contact:
Techmer PM LLC
Steve Loney
Phone: +1‐951-903-9111
Email:
sloney@techmerpm.com